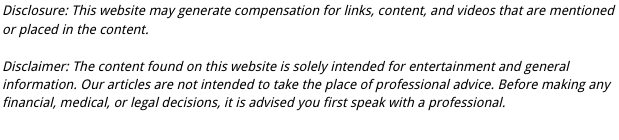
One of the new forms of construction is the high performance and impressive ICF or insulated concrete foam. While this may seem like a new concept to some, this has been around for quite some time. As a matter of fact, ICF systems have been used in global construction for over 60 years.
There are plenty of people new to the high performance capabilities of insulated concrete foam. However, they will soon learn that it is an inexpensive construction material that is wonderful for all parties involved. Here are all of the facts on insulated concrete foam and more!
High Performance Insulated Concrete Foam Is Inexpensive
First and foremost, it is important to understand that insulated concrete foam is incredibly inexpensive. As a result, homeowners and construction project managers will enjoy a less expensive construction process. Insulated concrete foam systems can cut final costs on a property by an estimate of $0.75 per square foot. While this does not seem like an immense amount of money on the surface it will eventually add up with time!
According to the United States Department of Housing and Urban Development, insulated concrete foam walls can save homeowners 20% to 25% on annual heating and cooling costs. Therefore, this means that homeowners will enjoy an inexpensive construction process that also helps them save money in the future. After all, so much money goes towards just paying for heating and cooling in terms of electricity!
High Performance Insulated Concrete Foam Is Great For Construction
Not only is insulated concrete foam an inexpensive material but it is also great for construction in general. Understand that insulated concrete foam decking will weight 40% less than the standard concrete flooring. Also, this decking is going to provide better insulation for the homeowners involved.
When constructing ICF walls, only one row is constructed at a time. End blocks are cut to fit to reduce waste. This reduced waste is not only going to save the construction project money but it also helps the environment as well. Reducing waste will prevent dangerous trash and waste from ending up in the ocean and potentially hurting animals.
Insulated concrete foam construction typically costs 40% less than the conventional basement construction due to reducing the number of steps. The reduced number of steps is going to shorten up the construction process. This is great for the homeowner and the construction workers involved as well. Visit http://monderlaw.com. It will help both parties and that is definitely best for business!
The average insulated concrete foam block is 10 inches in width. Therefore, buildings constructed with ICF are six to nine times stronger than traditional buildings. As a result, this high performance construction material is going to be great for anyone that has to deal with a natural disaster. So homeowners that live in an area that may suffer from a natural disaster will love this material.
Insulated concrete foam construction is capable of protecting properties from natural disasters because they’re capable of withstanding 402 kph winds. As a result, this is much stronger than a traditional building and can protect a home from serious damage. Anyone living in an area that may deal with natural disasters will definitely want to use this high performance construction material.
In Conclusion
The first foam concrete form was patented in 1966 by Werner Gregori, a Canadian contractor. The form measured at 16 inches high and 48 inches long. So anyone homeowner skeptical of using this type of construction material will surely want to get their hands on this insulated concrete foam. It will not only reduce the time and cost of a construction project but it will also help provide better results down the road as well!